Thermoset and thermoplastic material is often used for making various plastic parts, including knobs, handles, controls, containers and more. While these two types of plastic materials are alike, they are different in their chemical properties and therefore used in different applications, Each type has unique advantages and disadvantages in how they can be used and we will review each below.
What are the advantages of both Thermoset molding and Thermoplastic molding?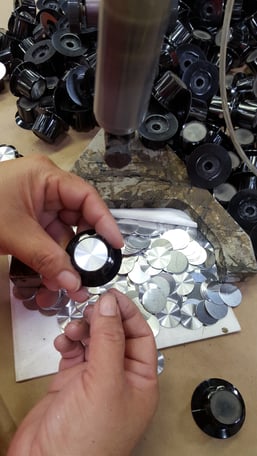
Thermoset materials offer excellent stability and resistance to high temperatures, making this material ideal for applications such as electrical components or industrial equipment that are subjected to harsher environments. Making thermoset parts also tends to be more cost-effective than other materials in high-volume production jobs, due to their ability to be molded quickly and with little to no waste.
Thermoplastic materials, on the other hand, offers greater flexibility and toughness, making them a popular choice for consumer products such as kitchen products or even toys. They can also be easily recycled, reducing their environmental waste and increasing their appeal to environmentally conscious consumers.
Despite their differences, both thermoset and thermoplastic materials are used in the creation of knobs, handles, and other components. Depending on the intended use and desired properties of the finished product, manufacturers can select the appropriate material and molding process to ensure a high-quality, durable product that meets the needs of their customers.
How does the process vary between Thermoset molding and Thermoplastic molding?
The process of creating knobs, handles and custom molded parts from thermoset and thermoplastic materials can vary depending on the desired outcome, but there are some general steps that are common between both types.
First, the material is selected based upon the specifications of the final product.
- Thermoset materials, such as epoxy or polyester, are ideal for components that require high heat resistance and stability at different sizes.
- Thermoplastic materials, such as polypropylene or polycarbonate, are better suited for applications requiring flexibility and toughness.
After the material is chosen, it's usually melted or combined with other components to make it better. These can be things like coloring or materials that make it stronger. For thermoplastics, this process is relatively simple, as the material can be melted and molded repeatedly without significant changes in its properties. In contrast, thermoset undergoes a chemical change through the compression molding process and as it hardens. This means it is really important to mix the ingredients carefully and keep the temperature and time just right to make sure it turns out correctly.
After the raw material is prepared, it is molded into a specific shape using an injection molding machine. Injection molding involves heating the material to a high temperature and injecting it into a mold under high pressure. The mold is designed into a desired shape including the details of the finished product, such as a textured grip or a threaded insert.
What are the options in finishing the molded product?
Once the material has cooled and become solid, the product is removed and finished. Finishing may involve:
- Trimming excess material
- Sanding rough edges
- Adding engravings or other markings
- Applying a coating or finish to improve the appearance or durability of the product
Creating knobs, handles, and other components from thermoset and thermoplastic materials is a relatively straight-forward process that requires expertise to execute properly at high volume. Attention to detail is crucial in order to achieve consistent quality and performance. When selecting the material and molding process, it's important to consider factors such as the component's intended use, expected lifespan, and any safety or regulatory requirements.